Application of water based ink in corrugated paper printing
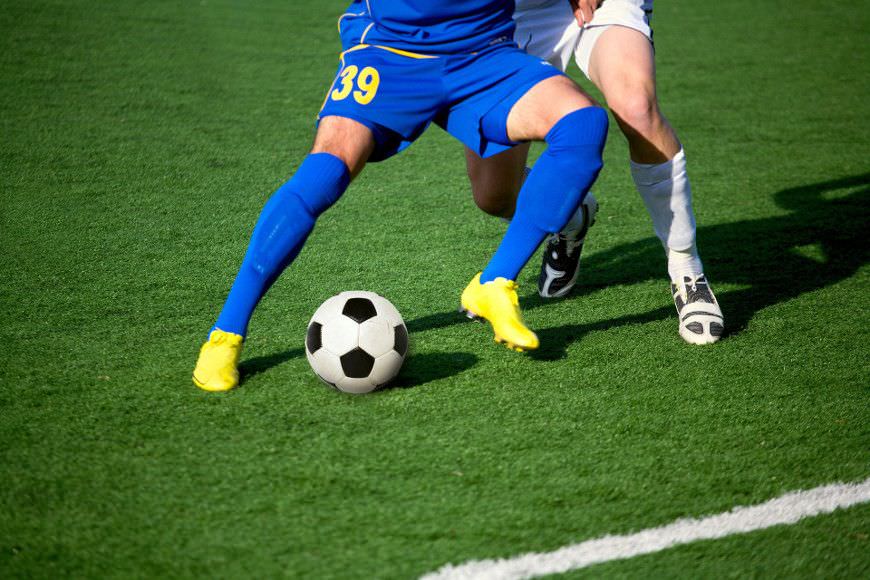
In the field of packaging printing, corrugated board printing occupies a large share. With the expansion of packaging market and the continuous improvement of printing technology, the quantity and quality of corrugated board printing have developed rapidly. However, more and more people are considering environmental factors, so the ink used in corrugated board printing has become a more concerned issue. In corrugated printing, the commonly used inks are solvent based ink, water-based ink and UV ink. Today, the editor of China paper network will give you a detailed introduction.
1. Common printing methods and inks of corrugated paper
Due to the corrugated paperboard with multi-layer wavy corrugated composite, poor surface flatness, printing pressure can not be too large, with screen printing can only print some simple patterns, text, printing is more difficult, so corrugated paperboard is generally printed with flexography. This is mainly because: (1) flexographic elastic deformation in the printing process can make up for the thickness error and uneven surface of corrugated paper, so that the printing ink color is uniform, so as to improve the quality of the finished product; (2) flexographic printing pressure is small, even after the plate compression deformation, it can better contact with the uneven thickness of corrugated board, and avoid thick part of the imprint paste, thin part of the poor contact The flexographic printing machine is simple in structure, which is easy to be combined with other processes, such as indentation, slotting, die-cutting, gluing, box making and so on.
When using flexography to print corrugated paper, the commonly used inks are solvent based inks, water-based inks and UV inks. With people's attention to environmental factors, the proportion of solvent based inks is decreasing year by year, while water-based inks and UV inks are becoming more and more popular. At present, the fastest growing water-based ink, the market share is also large, for example, in the United States about 90% of flexographic ink is water-based. In the flexible printing of corrugated boxes, water-based ink accounts for a larger proportion. This is because the words or simple patterns printed on corrugated boxes do not need high gloss, and water-based ink can meet the quality requirements of printed products. Moreover, corrugated boxes are interwoven fabrics with loose fibers, which have strong water absorption. After printing water-based ink, it is mainly permeable drying, and there is no need to set drying package And the water-based ink is non-toxic, harmless, non flammable, convenient and safe to use, low cost. Therefore, combined with these factors, flexo printing is the main printing method of corrugated paper, and the most commonly used ink is water-based ink.
2. Water based ink in corrugated printing
2.1 composition of water based ink
(1) Connecting material
The linking material in water-based ink is water-soluble resin and waterborne polymer emulsion. There are many kinds of waterborne resins, such as rosin maleic acid resin, styrene maleic acid resin, acrylic acid copolymer, ethyl acrylate and so on. Polymer emulsion, waterborne dispersing resin, has vinyl acetate copolymer, acrylic acid copolymer, polyurethane resin, epoxy resin and so on. At present, water-based acrylic resin is the most commonly used binder in water-based screen printing ink. The most successful acrylic polymers currently used are mainly four kinds of alkali soluble resin, acrylic emulsion, colloidal emulsion and solution, and special acrylic polymers.
(2) Pigment
Water based ink mainly uses organic or inorganic pigments with strong alkali resistance and good dispersibility in water system. These pigments are not only ordinary powder, but also pigment filter cake, pigment water-based dispersion and easily dispersed pigments in water. The pigment in water-based ink must have strong alkali resistance, high covering power, high color concentration and easy dispersion.
(3) Cosolvent
Due to the low solubility and wetting ability of water, it is necessary to select the corresponding cosolvent, such as ethanol, propanol (n, ISO), ethylene glycol monoacetic acid, etc. Through the addition of cosolvent can improve the shortcomings of the ink and improve its stability, can reduce the surface tension of water-based ink, increase the wetting of plastics, but also help to dissolve the resin, improve the drying speed. In addition, the resin is generally insoluble in water, and appropriate alkaline substances must be added to make the resin soluble in water. Generally, amines such as ethanolamine are selected, and the dosage depends on the pH value.
Komentarze